產(chǎn)線設備質量 鑒定背景
產(chǎn)線設備以系統(tǒng)集成與工藝穩(wěn)定性協(xié)同為核心原理,通過優(yōu)化生產(chǎn)節(jié)拍、定位精度及故障率,實現(xiàn)加工一致性、多工序協(xié)同與能耗控制的協(xié)同,廣泛應用于汽車總裝、電子組裝、食品包裝及醫(yī)藥生產(chǎn)等領域。在汽車焊接產(chǎn)線中,其用于多機器人協(xié)同作業(yè)的焊點精度控制;半導體封裝中,滿足晶圓傳輸?shù)奈⑽廴痉雷o;柔性產(chǎn)線中,保障多品種混流的快速切換。相較于單機設備,產(chǎn)線設備具有數(shù)據(jù)互聯(lián)、智能診斷及模塊化擴展等特性,是智能制造的核心載體。
中科檢測是具有法院入冊的產(chǎn)品質量鑒定服務機構,可以提供產(chǎn)線設備質量鑒定服務,擁有專業(yè)鑒定團隊和先進的儀器設備,為產(chǎn)線設備質量鑒定提供公正、準確的鑒定結果。
產(chǎn)線設備質量 鑒定爭議焦點
隨著產(chǎn)線智能化升級,相關質量糾紛案件顯著增加。司法爭議焦點集中于:
1、性能指標爭議:實際產(chǎn)能未達協(xié)議值、關鍵工位精度超標;
2、材料缺陷:傳輸帶耐磨壽命、伺服電機繞組絕緣等級不足;
3、工藝問題:多設備通信延遲、視覺檢測誤判率;
4、合同履約爭議:核心模塊(如進口PLC控制器、高精度傳感器)與技術協(xié)議不符。
此類案件需通過系統(tǒng)聯(lián)調(diào)測試、材料失效分析及動態(tài)負載驗證,明確質量責任歸屬。
產(chǎn)線設備質量 鑒定方法
產(chǎn)線設備訴訟質量鑒定主要包括以下技術方法:
1、設備性能檢測
對設備的各項性能指標進行檢測,包括生產(chǎn)效率、加工精度、穩(wěn)定性等。通過實際運行測試和數(shù)據(jù)分析,判斷設備是否達到技術合同規(guī)定的要求。
2、材料質量分析
對設備所使用的材料進行質量分析,檢測其物理性能、化學性能等指標。通過實驗室檢測和對比分析,確定材料是否符合相關標準和合同要求。
3、裝配與安裝檢查
檢查設備的裝配和安裝情況,包括零部件的安裝位置、連接方式、密封性能等。通過現(xiàn)場勘查和測量,判斷裝配和安裝是否符合工藝要求。
4、設計合理性評估
對設備的設計進行合理性評估,分析其結構設計、電氣系統(tǒng)設計等是否存在缺陷。通過專業(yè)的技術分析和模擬計算,評估設計對設備質量和性能的影響。
產(chǎn)線設備質量 鑒定案例
申請人某汽車廠與被申請人某集成商簽訂《車身焊接產(chǎn)線采購合同》,約定焊點精度±0.1mm。投產(chǎn)后焊點偏移率超15%,廠商辯稱系車間地基沉降導致。
鑒定分析結果:
質量分析專家組對“產(chǎn)線設備”的相關資料、合同技術協(xié)議、現(xiàn)場查勘案件材料等數(shù)據(jù)進行了討論和綜合技術分析,作出以下質量分析意見:
涉案產(chǎn)線設備的機器人重復定位精度±0.25mm(協(xié)議±0.1mm),視覺系統(tǒng)分辨率不足(像素誤差0.05mm);通信延遲1.2s(協(xié)議≤0.5s),導致協(xié)同誤差累積。
鑒定結論認定設備控制算法與傳感系統(tǒng)缺陷是質量主因。
產(chǎn)線設備質量 鑒定報告內(nèi)容
產(chǎn)線設備質量鑒定報告應包含:
1、鑒定目的(如生產(chǎn)事故歸因、技術合規(guī)性驗證)及引用標準;
2、涉案設備型號、軟件版本、運維日志;
3、檢測方法及設備清單(如激光跟蹤儀、功率分析儀);
4、檢測數(shù)據(jù)與失效關聯(lián)性分析(如通信延遲對精度的影響);
5、明確質量責任判定結論及技術依據(jù);
6、鑒定人員簽名、自動化工程師資質證明及機構公章。
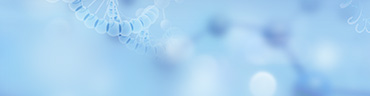
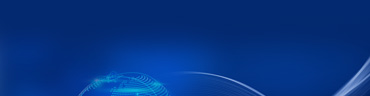